Introduction
Etch is a process that removes
materials that are not protected by hardened photoresist from the wafer surface
to achieve the IC design requirements. Two main etching techniques are:
Wet Chemical Etching
- A buffered oxide etch is commonly used to etch
windows in silicon dioxide layers. BOE is a solution containing HF and
submerging the wafers in the solution performs etching.
- Etch rate is temperature dependent, and
temperature is carefully monitored during the etch process.
- Wet chemical etching tends to be an isotropic
process; etching takes place equally in all directions.
- Fig. 1(a) shows the result of isotropic
etching of a narrow line in silicon dioxide. The etching process has
etched under the resist by a distance equal to the thickness of the film.
This “etch bias” becomes a serious problem in processes requiring
linewidths with dimensions similar to the thickness of the film.[1]
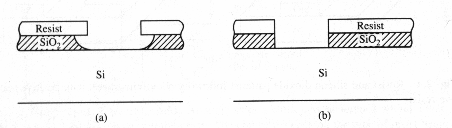
Fig. 1
Etching profiles obtained with (a) isotropic wet chemical etching and (b) dry
anisotropic etching in a plasma or reactive ion etching system. [1]
Dry Etching
- Dry etching processes are widely use in VLSI
fabrication.
- Highly anisotropic etching profiles can be
obtained as shown in Fig. (b).
- Plasma etching immerses the wafers in gaseous
plasma created by RF excitation in a vacuum system.
- Sputter etching uses energetic noble gas ions
such as Ar+ to bombard the wafer surface. Etching occurs by
physically knocking out atoms off the surface of the wafer.
- Reactive ion etching combines the plasma and
sputter etching processes.
- Plasma systems are used to ionize reactive
gases, and the ions are accelerated to hit the surface. Etching occurs
through a combination of the chemical reaction and momentum transfer from
the etching species.[1]